There is something timeless and classic about trains that captured the imagination of Mark Ritchie early in his career; that has stayed with him for more than 20 years.
Manager of Transportation and Logistics for Heartland Polymers, Ritchie and his team were responsible for designing, establishing and connecting the infrastructure to support the complex transportation and logistics requirements of the market’s newest global polypropylene producer. Moving from greenfield and ideas on paper to the reality of 1,600 railcars, and port and freight agreements, has taken several years and lots of teamwork. It was a massive undertaking, and looking back, Ritchie is proud of what his small team accomplished through a global pandemic.
“We had the rare opportunity with a new build to take the best of everything and integrate it into our operations from the very start”Mark Ritchie, Manager, Transportation and Logistics
Success is in the Details
“Our task was to develop the infrastructure required to distribute our product when we’re commercially up and running,” explains Ritchie, who worked for 12 years with Canadian Pacific Railway helping to manage logistics for major commodities prior to joining the Heartland team.
“My job was to coordinate the efforts to get the logistics infrastructure in place. That was everything from the freight agreements with the rail carriers, negotiating the track construction agreement to connect Heartland Petrochemical Complex to the North American rail network. It was getting rail cars procured and then leased. We got our storage in transit (SIT) yard infrastructure in Canada and the U.S. Then beyond that is the US freight agreements and also our export packaging agreements in Vancouver and the Southeast US. It started with figuring out what the landscape looked like, what our options were, and then narrowing it down to making recommendations and ultimately landing on what we have today.”
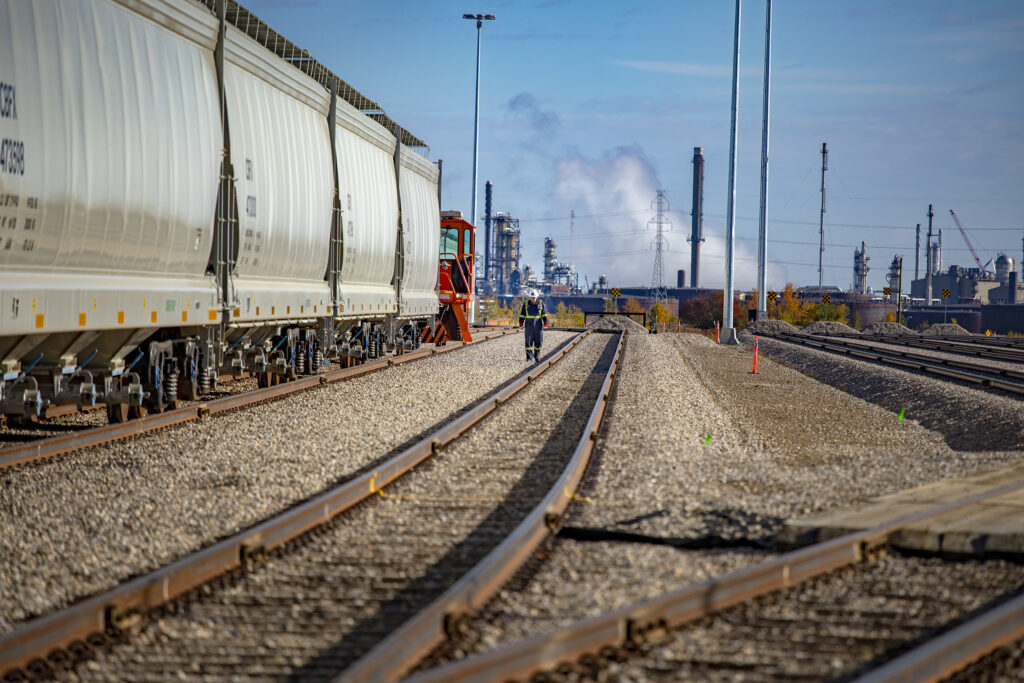
Building a transportation network from the ground up was “the opportunity of a lifetime”, says Ritchie, who credits his team with bringing highly specialized experience across contract management, customs, procurement, site management, strategy development and market analysis, as well as fleet and maintenance. A philosophy of “better” underlined every step of the development process.
“We had the rare opportunity with a new build to take the best of everything and integrate it into our operations from the very start: the best technology, the best systems, the best practices and procedures that we’ve learned from this and many other industries,” he explains. “Our mantra was to operate then optimize. First, we wanted to establish infrastructure that would allow us to operate and execute on our two primary goals of maintaining production and moving product to market. Now that we’re operating and we have an understanding, the next phase will be to look back at the decisions that we made and decide where we can improve.”
What It Means for Heartland’s Customers
Heartland took advantage of technology advances to outfit the entire railcar fleet with leading edge GPS, which provides the company and its customers with unique new features: real-time tracking for delivery schedules, sensors on hatches to determine when they’re open, sensors that determine the load level on each car and temperature sensors. But that’s just one aspect of the leading technology employed at site and throughout the entire logistics journey. Another example is the state-of-the-art system for washing and loading 1,600 cars to keep everything on time – and integrating Operation Clean Sweep, the industry program aimed at achieving zero plastic resin loss.
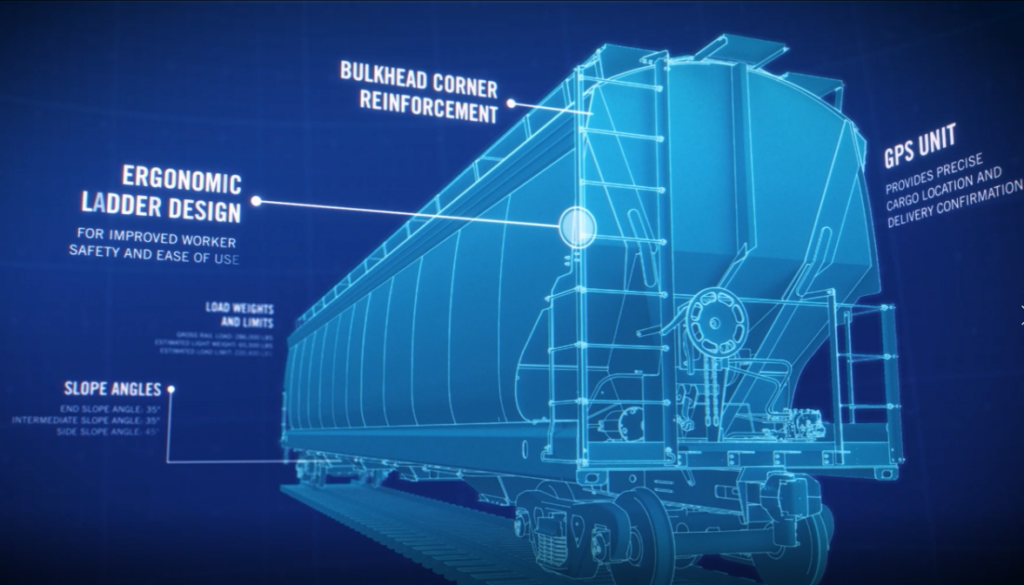
We’re Ready
Ritchie and his team were ecstatic to see the first cars start rolling down the line when the Heartland Complex commissioned the polypropylene (PP) facility this past July.
“The number one job our team has is to ensure continuity of production at the plant and getting that product to the ultimate markets where it needs to be consumed. We’re excited to see that all come together with these first shipments.”